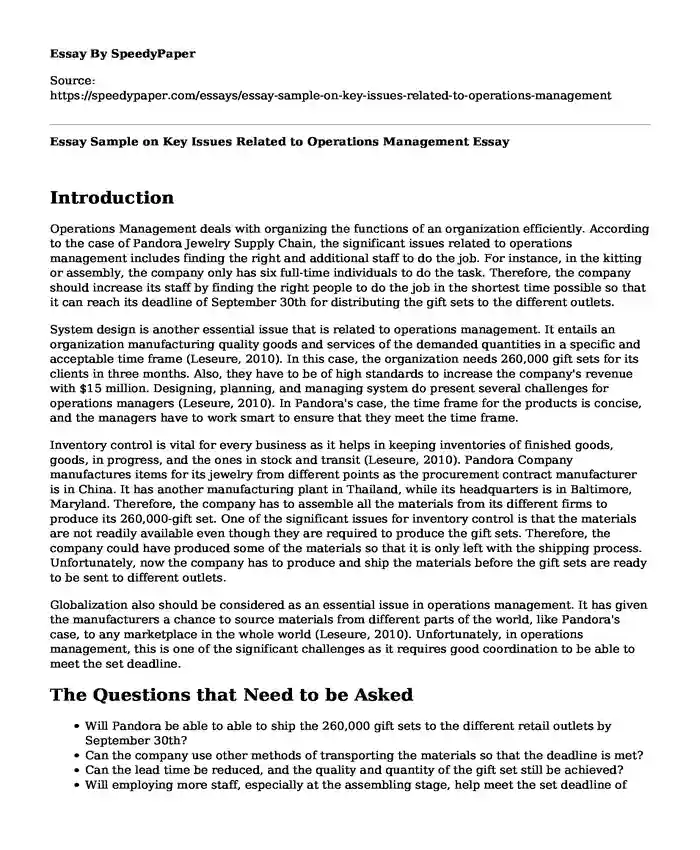
Type of paper:Â | Essay |
Categories:Â | Supply chain management |
Pages: | 5 |
Wordcount: | 1115 words |
Introduction
Operations Management deals with organizing the functions of an organization efficiently. According to the case of Pandora Jewelry Supply Chain, the significant issues related to operations management includes finding the right and additional staff to do the job. For instance, in the kitting or assembly, the company only has six full-time individuals to do the task. Therefore, the company should increase its staff by finding the right people to do the job in the shortest time possible so that it can reach its deadline of September 30th for distributing the gift sets to the different outlets.
System design is another essential issue that is related to operations management. It entails an organization manufacturing quality goods and services of the demanded quantities in a specific and acceptable time frame (Leseure, 2010). In this case, the organization needs 260,000 gift sets for its clients in three months. Also, they have to be of high standards to increase the company's revenue with $15 million. Designing, planning, and managing system do present several challenges for operations managers (Leseure, 2010). In Pandora's case, the time frame for the products is concise, and the managers have to work smart to ensure that they meet the time frame.
Inventory control is vital for every business as it helps in keeping inventories of finished goods, goods, in progress, and the ones in stock and transit (Leseure, 2010). Pandora Company manufactures items for its jewelry from different points as the procurement contract manufacturer is in China. It has another manufacturing plant in Thailand, while its headquarters is in Baltimore, Maryland. Therefore, the company has to assemble all the materials from its different firms to produce its 260,000-gift set. One of the significant issues for inventory control is that the materials are not readily available even though they are required to produce the gift sets. Therefore, the company could have produced some of the materials so that it is only left with the shipping process. Unfortunately, now the company has to produce and ship the materials before the gift sets are ready to be sent to different outlets.
Globalization also should be considered as an essential issue in operations management. It has given the manufacturers a chance to source materials from different parts of the world, like Pandora's case, to any marketplace in the whole world (Leseure, 2010). Unfortunately, in operations management, this is one of the significant challenges as it requires good coordination to be able to meet the set deadline.
The Questions that Need to be Asked
- Will Pandora be able to able to ship the 260,000 gift sets to the different retail outlets by September 30th?
- Can the company use other methods of transporting the materials so that the deadline is met?
- Can the lead time be reduced, and the quality and quantity of the gift set still be achieved?
- Will employing more staff, especially at the assembling stage, help meet the set deadline of September 30th?
The Major Tradeoffs
The first major tradeoff is getting additional machinery for tweaking the already made porcelain box as they need some adjustments in accommodating gift sets configuring. Even though the machinery might be expensive, they will help produce them in about two weeks and then ship them in 5 weeks. Furthermore, changing the boxes' transportation method from ocean to air is a good option for meeting the set deadline. Although it may require additional cost, its worth as it will ensure that the other processes are completed on time, and the clients get their goods. Another tradeoff is to have additional staff at the kitting or assembly stage to meet the company's deadline of 3 months. Working overtime is also an option, but it might not be effective since the quality of the gift sets might be compromised when the staff gets tired. If the employees are working on their own, then they will need about two months three days to complete assembling the gift sets working 8 hours a day.
Some Solutions that Will Ensure that the September 30th Deadline is Met
The first solution is in the Procurement department, and it entails purchasing additional machinery to help tweak the porcelain box that is already in production. Even though the company will incur costs, it will reduce the lead time of producing the boxes by half. Therefore, the boxes will be ready in 3 weeks. Another solution is that instead of shipping the boxes through sea freight, which needs five weeks of ocean transit time, air transportation can be used. According to Sales (2013), it is considered the fastest shipping method, highly reliable, cargo can be sent anywhere, low insurance premium, less requirement for warehousing, high-security level, and one can easily follow the cargo's status. On the demand or supply planning, the six weeks lead time cannot be changed since, in the forecast of the factory, the gift sets were not initially considered.
Another solution that the company can consider is by employing additional staff at the kitting or assembly stage. Currently, the kitting team has a full-time headcount of six individuals, and every kitter can only assemble about 85 gift sets in one hour. If the six personnel are working 8 hours daily, then they will make 4080 gift sets in a day. Unfortunately, they are required to make 260,000 gift sets. Therefore, it will take them 64 days to make all the gift sets assuming they work even during weekends. Employing an additional staff of 6 people will play a major role in reducing the assembly lead time by half without compromising the quality of the gift boxes (Levi, 2014). It is vital to employ additional staff to enhance productivity and even lead to excellent business results. If the other employees see that they have additional team members, they will be motivated, and their morale boosted (Levi, 2014). Initially, they might argue that completing 260,000 boxes will take centuries, but with additional personnel, they will be provided with an extra energy boost. Working with the additional team also makes the team members have a feeling of belonging as they are part of a communal objective (Levi, 2014). Working in a big team will benefit the company and make the members learn fast and relive stress (Levi, 2014). After completing the assembly process, the company will have sufficient time to carry outbound shipping to warehouse stores using a large parcel carrier. Therefore, these solutions are essential for the company in ensuring that the deadline is met and the customers get their gift boxes on time. In the end, the company's revenue will be increased, and customers satisfied.
References
Leseure, M. (2010). Key concepts in operations management. Los Angeles: SAGE.
Levi, D. (2014). Group dynamics for teams. Thousand Oaks, Calif. SAGE
Sales, M. (2013). The air logistics handbook: Airfreight and the global supply chain. Routledge.
Cite this page
Essay Sample on Key Issues Related to Operations Management. (2023, Sep 17). Retrieved from https://speedypaper.net/essays/essay-sample-on-key-issues-related-to-operations-management
Request Removal
If you are the original author of this essay and no longer wish to have it published on the SpeedyPaper website, please click below to request its removal:
- Free Essay on Project Management and Project Idea
- Essay Example: Bargaining Power of Suppliers for Nike
- Essay Sample. Employees' Social Media Use: Problem at Workplace
- Paper Example. People and the Process of Change
- Paper Example. Starbucks China: Managing Growth Through Innovation
- Essay Example - A Personal Conflict
- The Five Fabulous Fashion Nights in New York - Free Essay
Popular categories