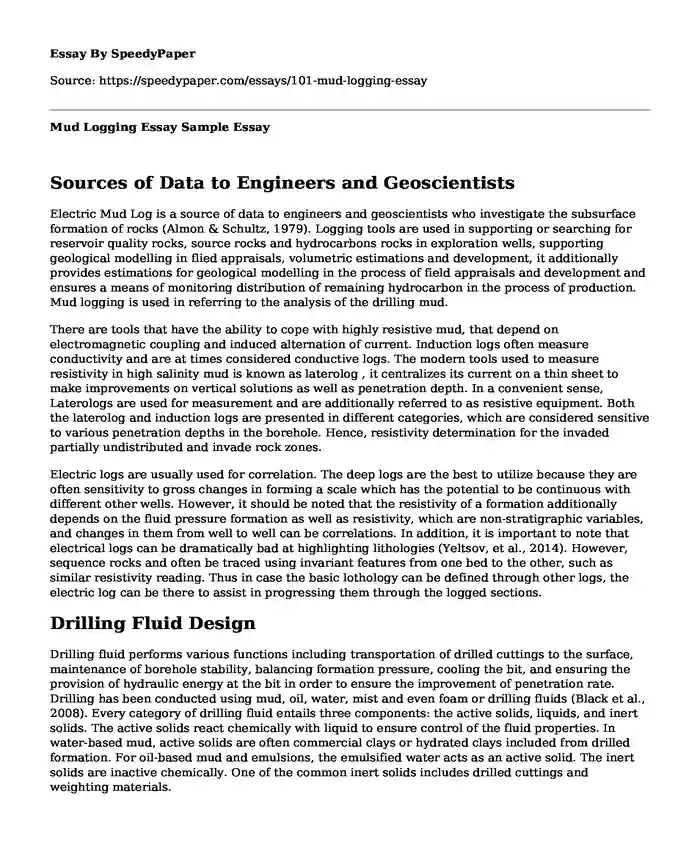
Type of paper:Â | Essay |
Categories:Â | Engineering Physics |
Pages: | 7 |
Wordcount: | 1739 words |
Sources of Data to Engineers and Geoscientists
Electric Mud Log is a source of data to engineers and geoscientists who investigate the subsurface formation of rocks (Almon & Schultz, 1979). Logging tools are used in supporting or searching for reservoir quality rocks, source rocks and hydrocarbons rocks in exploration wells, supporting geological modelling in flied appraisals, volumetric estimations and development, it additionally provides estimations for geological modelling in the process of field appraisals and development and ensures a means of monitoring distribution of remaining hydrocarbon in the process of production. Mud logging is used in referring to the analysis of the drilling mud.
There are tools that have the ability to cope with highly resistive mud, that depend on electromagnetic coupling and induced alternation of current. Induction logs often measure conductivity and are at times considered conductive logs. The modern tools used to measure resistivity in high salinity mud is known as laterolog , it centralizes its current on a thin sheet to make improvements on vertical solutions as well as penetration depth. In a convenient sense, Laterologs are used for measurement and are additionally referred to as resistive equipment. Both the laterolog and induction logs are presented in different categories, which are considered sensitive to various penetration depths in the borehole. Hence, resistivity determination for the invaded partially undistributed and invade rock zones.
Electric logs are usually used for correlation. The deep logs are the best to utilize because they are often sensitivity to gross changes in forming a scale which has the potential to be continuous with different other wells. However, it should be noted that the resistivity of a formation additionally depends on the fluid pressure formation as well as resistivity, which are non-stratigraphic variables, and changes in them from well to well can be correlations. In addition, it is important to note that electrical logs can be dramatically bad at highlighting lithologies (Yeltsov, et al., 2014). However, sequence rocks and often be traced using invariant features from one bed to the other, such as similar resistivity reading. Thus in case the basic lothology can be defined through other logs, the electric log can be there to assist in progressing them through the logged sections.
Drilling Fluid Design
Drilling fluid performs various functions including transportation of drilled cuttings to the surface, maintenance of borehole stability, balancing formation pressure, cooling the bit, and ensuring the provision of hydraulic energy at the bit in order to ensure the improvement of penetration rate. Drilling has been conducted using mud, oil, water, mist and even foam or drilling fluids (Black et al., 2008). Every category of drilling fluid entails three components: the active solids, liquids, and inert solids. The active solids react chemically with liquid to ensure control of the fluid properties. In water-based mud, active solids are often commercial clays or hydrated clays included from drilled formation. For oil-based mud and emulsions, the emulsified water acts as an active solid. The inert solids are inactive chemically. One of the common inert solids includes drilled cuttings and weighting materials.
Historically, drilling fluid was used in the mid-1800s in cable tool drilling for suspending the cuttings until bailed from the drilled hole. With the drilling advent in the water, well-drilling industries, drilling fluid as well understood to cool the drill bit and for suspending drilled cuttings for elimination from the wellbore. Clays were additionally added to the drilling fluid by 1890s ad by the time Spindle top was discovered, it was rendered necessary in order to suspend solids in the drilling fluid to provide support for the walls of the boreholes. The solids came as a result of disaggregation of formations penetrated with the help of the drill bit. The drilling fluid was recruited and waste was added in order to maintain an approximate weight as well as viscosity for particular drilling conditions. Pieces of formation that were dissolved using water were removed from the drilling fluid to continue the operation.
The main objective in drilling fluid design is maintaining the stability of a hole. In any case, the hole enlarges, higher viscosity and strength of the gel will be necessary, which will result in decreased rates of penetration. The conflict involved in these rheological requirements will be reduced using a shear-thinning mud, which sets a gel sufficient enough to provide suspense for cuttings when circulations stop but also breaks up fast in mud when distributed. Such a drilling fluid has high yield points or plastic viscosity ratio. When designing a drilling fluid, the circulation fluid has impacts on every aspect of drilling, logging cost, and cement. The drill needs to be designed carefully in order to maintain the stability of a wellbore and to perform several other functions as well. The mud for every section that has specified physical and chemicals features need to be kept as designed. Anything defining the path that should be followed by the wellbore has to be known. Diagrams that shows well profile from the side and from above need to be included.
Drill Stem Test (DST)
A Drill Stem Test (DST) is conducted when oil shows are traced in cutting; this can take place several times in the drilling of a particular explanatory well. It enables the production capacity of an encouraged formation to undergo testing in a borehole full of drilling mud. The testing tool assembly attached to the lower parts of the string of the drill pipe is lowered and positions opposite to the reservoir rock, isolated through an expandable packer, relieved of the clump pressure on mad which is allowed to produce with the help of drill stem (Dias et al., 2014). They hydrostatic force perceived from the mud column within the hole is often great compared to the formation pressure of the production zone that is supposed to be under test. The basic drill stem test tool assembly entails the following:
A test valve (upper-pressure recorder) to ensure control of mudflow into the drill pipe (or exclude mud) in the process of entry into the hole as it allows for formed fluids to enter in the process of testing. The hydraulic jar is set underneath a tester valve to increase pressure to 8psi, in order to release the packer after the testing is done.
A rubber packer which is increased against the hole to ensure a separation between the annual sector above and below the zone encountered.
Equalizing bypass value allows for pressure from mud to equalize across the packer in and out of the DST arrangement after the flow test is complete
A pressure recorder which obtains quantitative results in the flow of pressure period or pressure formation is applied, following the way in which the formation fluid is allowed. Pressure recorders furnish an entire record of events that take place during a specific test ad are in forms of graphs of pressure time.
Theoretical Analysis
Muskat (1937) suggested the following form of differential equation that could help in solving problems which applies to Drill Stem Test (DST) horizontal radial flow through unit thickness of production of formation
(∂^2 p)/(∂r^2 )+1/r ∂p/∂^r =(/cμ)/k ∂p/∂t
Where r= the distance of the center of the well (L)
p= pressure formation (F/L2)
/= the porosity of the production formation
c= the compressibility of the fluid (L2/F)
μ= the fluid viscosity (FT/L2)
k= the permeability (L2)
The concept of storage as highlighted in this equation is somehow different from the concept used in ground water theory. Storage is expressed in the first equation by the factors / and c, which include simply compatibility of fluid in production formation
Two pressure recorders are often used in measuring the inside pressure and the perforated anchor on the outside. The two measurements allow for accurate estimations of if or not the perforations have been plugged in the process of testing. A perforated anchor includes an extension below the tool that provides support for the weight which is applied in order to set the packer. It often rests at the bottom of the hole within an open–hole test or in a cement plug within the desired location. Safety joints are equipped to afford a way of unscrewing the drill string at a point convenient for fishing operation, in case the packer is stuck. The another safety joint is added underneath with an aim of preventing the DST assembly from sticking (Round, 1996). It is important to note that after drill stems is at the bottom, and the required operation is completed, the packer compresses and expands and is isolated within the lower zone or the required location from the rest of the open hole.
Open Hole Completion
Open hole completion is used when oil reservoir is exposed during completion of a straight or horizontal well. Open hole completion is suitable for thick oil reservoir. In case a gas cap on the top or water-bearing beds close to the top boundary exists, the intermediate casing can be run across the oil-gas interface and the upper part of the oil reservoir is sealed followed by open hole completion. Open hole completion is used typically in the component formation such as limestone, dolomite and consolidates sandstone that stands unsupported in a borehole. When used, casting is set at the top of a production zone. The production interval is then drilled. This completion category is often used when producing interval is strong and component, so that it does not cave in or otherwise final to function. Open hole completions can additionally be used in deviated, horizontal or vertical wells. One advantage of using open completion is that the while formation interval is exposed to the wellbore.
Tubing Design
Tubing is a pipe positioned in the well in order to inject fluids. The proper selection of size, connection and grade are essential to the wellbore completion program. Tubing has to be designed in order to resist failure from axial or compressive forces, internal and external pressure, corrosion and buckling. Tubing design depends on the selection of the most economical grades and wall thicknesses (mass unit of tubing) which will withstand, without failing , the forces of that tubing exposes through expected tubing life. A design factor for tension should be approximately 1.4-1.6. The collapse design factor has to be less than 1.0, assuming an annulus filled with fluid and evacuated tubing. The design factor for burst cannot be less than 1.1.
Cite this page
Mud Logging Essay Sample. (2018, Sep 19). Retrieved from https://speedypaper.net/essays/101-mud-logging-essay
Request Removal
If you are the original author of this essay and no longer wish to have it published on the SpeedyPaper website, please click below to request its removal:
- Clarity of the Law in Decision-Making Process - Essay Example
- HR Essay Example: Diversity in Organizations
- Naturalistic Observation - Essay Sample on Eye Contact
- Essay Sample That Contains Cosmopolitan Magazine Analysis
- Free Example of Annotated Bibliography on Child Homelessness
- Essay Sample on Charles Conaway: Ethical Failures
- Literary Analysis Essay on From a Sand County Almanac: Sustainability and Conservation
Popular categories